
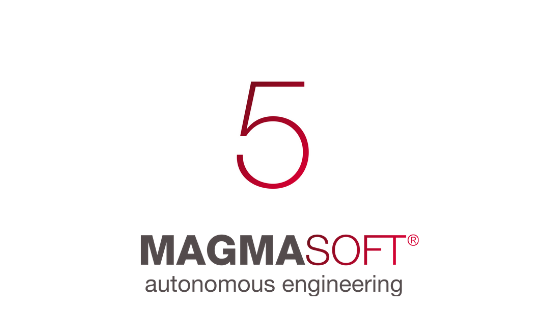
Users should refer to the original published version of the material for the full abstract. In order to compensate for shrinkage, foundries include reservoirs of metal, called risers, along the gating.

Steel is often poured near 3,000 degrees Fahrenheit, and as it cools in a mold, it shrinks. No warranty is given about the accuracy of the copy. Solidification simulation software, like MAGMASOFT, shows how metal will enter a mold cavity and behave as it cools. However, users may print, download, or email articles for individual use.
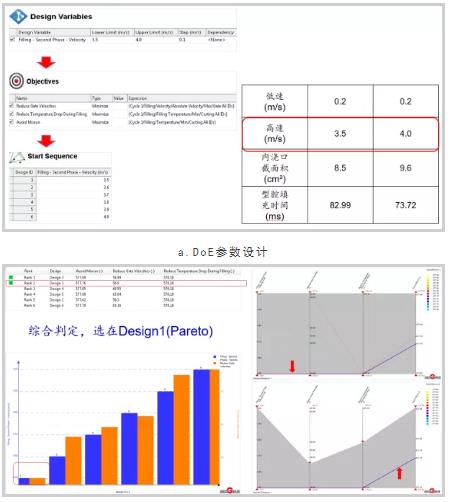
Solidification simulation is an essential tool for the modern methods engineer. MAGMAproject supports you in designing robust products and processes within the scope of your degrees of freedom. With strong CAE support from our R&D department (Abaqus, Tosca, FeSafe, MagmaSoft, AVL Fire) Reduced development time and better, quality and cost optimized parts. Close cooperation between engineers from R&D, design and technology. Feeding occurs by having a “reservoir” of liquid metal available that fills the cavities that would otherwise form during solidification. Our experts compile and document step-by-step improvements and potential solutions - from a simple solidification simulation, to a full factorial design of experiments (DoE) or an autonomous optimization of your casting process. All developement activities, from part to process, are carried out simultaneously. The supply of compensating liquid metal to a casting during cooling and solidification is known as feeding. If this contraction, or shrinkage, is not compensated for, the result is a defect in the form of a cavity in the cast shape that could render the component unsuitable for use. These products must be able to withstand high moulding pressures, be simple to apply and provide consistent feed performance.ĭuring solidification and cooling, liquid metals and alloys contract as they pass from the liquid state into solid.
#DOE MAGMASOFT SOFTWARE#
High-strength, high-pressure, automatic moulding lines place extra demands on feeder sleeve products. After gating and rigging the castings we use MAGMASOFT solidification software to analyze the gating and rigging solution to ensure that we engineer a high. Using MAGMASOFT, foundries can compare the cost benefit of sleeves from various suppliers. Here a comparison between two suppliers is conducted on the soundness and the resulting costs between the sleeves. Can a foundry benefit from a more expensive yet better performing sleeve?Īt what point does the yield benefit outweigh the cost benefit?
